Implemented design codes for bolted joints
Steel code
The following codes have been implemented in CYPECAD, CYPE 3D and Integrated 3D structures of CYPECAD for the design of bolted joints:
- ABNT NBR 8800 (Brazil)
- ABNT NBR 8800:2008 (Brazil)
- ANSI/AISC 360-05 (LRFD) (USA - International)
- ANSI/AISC 360-10 (LRFD) (USA - International)
- CTE DB SE-A (Spain)
- EAE (Spain)
- Eurocode 3 EN 1993-1-8:2005 (General Document)
- Eurocode 3 NF EN 1993-1-8/NA:2007-07 (With National Application Document for France)
- Eurocode 3 NP EN 1993-1-8:2005/NA:2010 (With National Application Document for Portugal)
- Eurocode 3 UNI EN 1993-1-8:2005 (General Document adapted to Italy)
- IS 800:2007 (India)
- NTC: 14-01-2008 (Italy)
The corrections carried out by the European Committee for Standardization on Eurocode 3 (EN 1993-1-8:2005 / AC:2009) have also been implemented.
Bolt series
The available bolt series, depends on the steel code used for the design. These are indicated in the table below:
Steel codes |
Prestressed
bolt series |
Ordinary bolt series |
ABNT NBR 8800 (Brazil)
ABNT NBR 8800:2008 (Brazil) |
ASTM A307
ASTM A325
ASTM A490
ASTM A325 M
ASTM A490 M
ISO 4016 |
ASTM A325
ASTM A490
ASTM A325 M
ASTM A490 M |
ANSI/AISC 360-05 (LRFD) (USA - International)
ANSI/AISC 360-10 (LRFD) (USA - International) |
ASTM A307
ASTM A325
ASTM A490
ASTM A325 M
ASTM A490 M |
CTE DB SE-A (Spain)
EAE (Spain)
Eurocode 3 EN 1993-1-8:2005 (General Document)
Eurocode 3 NF EN 1993-1-8/NA:2007-07 (With NAD for France)
Eurocode 3 NP EN 1993-1-8:2005/NA:2010 (With NAD for Portugal)
Eurocode 3 UNI EN 1993-1-8:2005 (General Document adapted to Italy)
NTC: 14-01-2008 (Italy) |
ISO 7411
ISO 7412
EN 14399-3, HR System
EN 14399-4, HV System |
ISO 4014
ISO 4017 |
IS 800:2007 (India) |
ISO 7411
ISO 7412 |
Types of implemented bolted connections
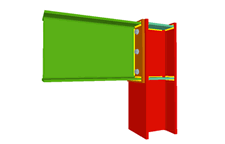
Column to beam bolted moment connection using front plate (at last span of column)
|
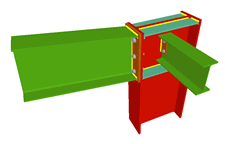
Column to beam bolted moment connection using front plate with simply connected orthogonal beam using lateral plate (at last span of column)
|
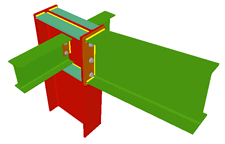
Column to beam moment connection using front plate with two simply connected orthogonal beams using lateral plates (at last span of column)
|
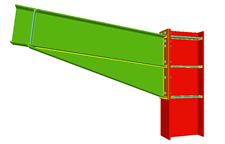
Column to beam bolted moment connection with haunch using front plate (at last span of column)
|
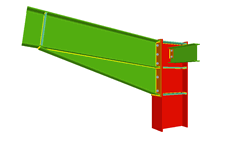
Column to beam bolted moment connection with haunch using front plate and simply connected orthogonal beam using lateral plate (at last span of column)
|
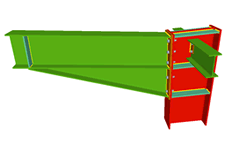
Column to beam bolted moment connection with haunch using front plate and two simply connected orthogonal beams using lateral plates (at last span of column)
|
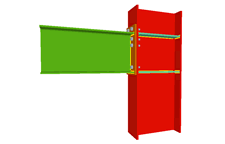
Column to beam bolted moment connection using front plate (continuous column)
|
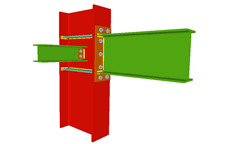
Column to beam bolted moment connection using front plate with simply connected orthogonal beam using lateral plate (continuous column)
|
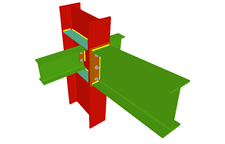
Column to beam bolted moment connection using front plate with two simply connected orthogonal beams using lateral plates (continuous column)
|
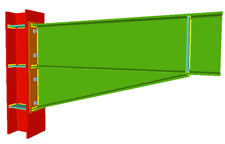
Column to beam bolted moment connection with haunch using front plate (continuous column)
|
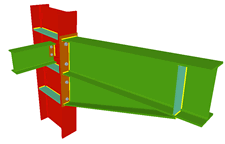
Column to beam bolted moment connection with haunch using front plate and simply connected orthogonal beam using lateral plate (continuous column)
|
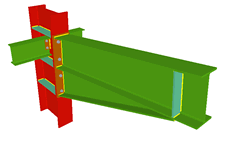
Column to beam bolted moment connection with haunch using front plate and two simply connected orthogonal beams using lateral plates (continuous column)
|
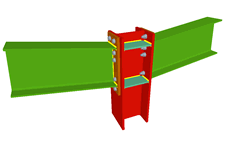
Column to two beam bolted moment connection using front plates (at last span of column)
|
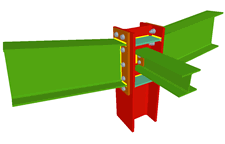
Column to two beam bolted moment connection using front plates and simply connected orthogonal beam using lateral plate (at last span of column)
|
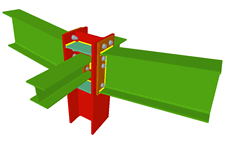
Column to two beam bolted moment connection using front plates and two simply connected orthogonal beams using lateral plates (at last span of column)
|
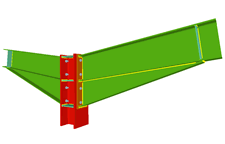
Column to two beam bolted moment connection with haunches using front plates (at last span of column)
|
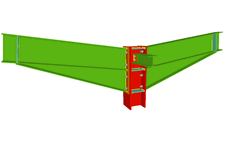
Column to two beam bolted moment connection with haunches using front plates and simply connected orthogonal beam using lateral plate (at last span of column)
|
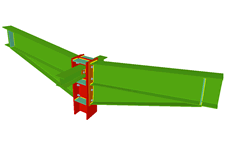
Column to two beam bolted moment connection with haunches using front plates and two simply connected orthogonal beams using lateral plates (at last span of column)
|
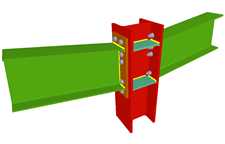
Column to two beam bolted moment connection using front plates (continuous column)
|
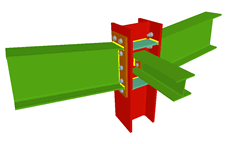
Column to two beam bolted moment connection using front plates and simply connected orthogonal beam using lateral plate (continuous column)
|
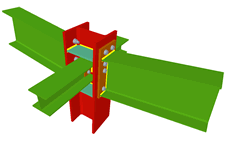
Column to two beam bolted moment connection using front plates and two simply connected orthogonal beams using lateral plates (continuous column)
|
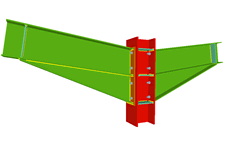
Column to two beam bolted moment connection with haunches using front plates (continuous column)
|
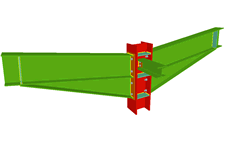
Column to two beam bolted moment connection with haunches using front plates and simply connected orthogonal beam using lateral plate (continuous column)
|
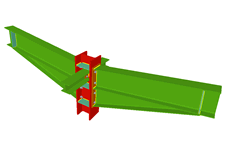
column to two beam bolted moment connection with haunches using front plates and two simply connected orthogonal beams using lateral plates (continuous column)
|
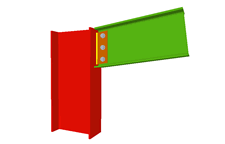
Column to beam bolted simple connection using lateral plate (at last span of column)
|
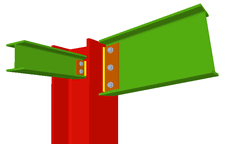
Column to beam bolted connection using lateral plate with simply connected orthogonal beam using lateral plate (at last span of column)
|
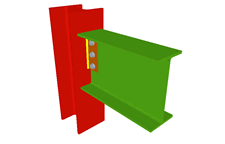
Column to beam bolted simple connection using lateral plate (continuous column)
|
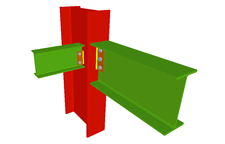
Column to beam bolted simple connection using lateral plate and simply connected orthogonal beam using lateral plate (continuous column)
|
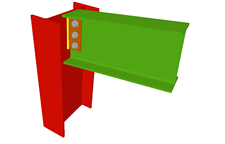
Beam to column web bolted simple connection using lateral plate (at last span of column)
|
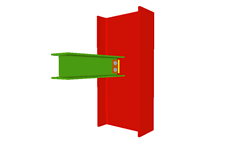
Beam to column web bolted simple connection using lateral plate (continuous column)
|
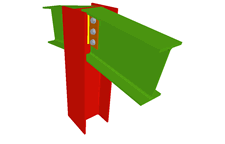
Two beam to column web bolted simple connection using lateral plates (at last span of column)
|
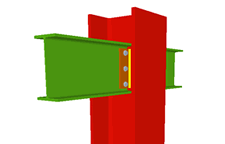
Two beam to column web bolted simple connection using lateral plates (continuous column)
|
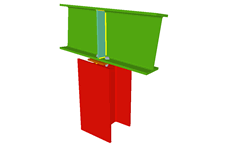
Continuous beam supported by column using simple lateral plate connection (beam web perpendicular to column web)
|
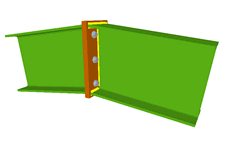
Bolted ridge connection using front plates
|
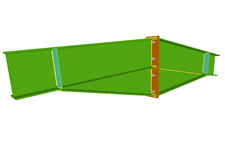
Bolted ridge connection with haunches using front plates
|
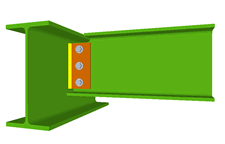
Beam to beam bolted simple connection using lateral plate
|
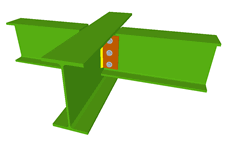
Beam to beam bolted simple connection using lateral plates
|
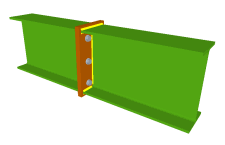
Beam to beam (same section) splice connection using front plates
|
|
(1) Joints with continuous columns can only be introduced in CYPE 3D and in Integrated 3D structures of CYPECAD. In CYPECAD, only columns in transition or ends of columns can have this joint.
Design options
The design options for welded and bolted connections may be configured in the Options menu
(Joints > Options). This dialogue box can be accessed via the following menu options:
- In CYPECAD and its Integrated 3D structures:
- Beam Definition tab > Job > Joint analysis options
- Results tab > Joints > Joint analysis options
- In CYPE 3D:
This dialogue box contains three tabs:
- Non-prestressed bolts
Contains the design options for non-prestressed bolts (Bolt series code, Bolt steel class
and Available diameters). Options selected here will only affect bolted connection design.
- Prestressed bolts
Contains the design options for prestressed bolts (Bolt series code, Bolt steel class, Available
diameters and Friction surface class). Additionally, the type of friction
surface must be indicated to check the bolt for slipping. Within this dialogue, the program
also defines the properties of the selected surface in accordance with the article of the
selected code. Options selected here will only affect bolted connection design.
- Stiffeners
Contains two option groups which configure the layout of the stiffeners:
- Stiffeners at haunch ends
Contains two options which when activated force the program to always provide stiffeners,
one in column to beam connections and the other in ridge connections. Affects welded connections
designed with the Joints I module and bolted connections designed with the Joints
II module.
Regardless of whether this option is activated or not, the program always provides stiffeners
at the ends of the haunches if the design requires their presence.
- Stiffeners for beams fixed to the column web
Activates the trimming of stiffeners for beams fixed to column webs. It only affects welded
connections designed with the Joints
III module and bolted connections using the Joints
IV module (the other modules do not contemplate
connections consisting of beams fixed to column webs).
This option does not imply changes
in the structural check but only takes into account aspects related to the aesthetics and
with the number of trimming operations undertaken in the fabrication process. Upon activating
the trimming option, it will be carried out if the following conditions are met:
- The smallest side of the trim has to be greater than 10mm.
- The angle formed between the inclined side of the trim and the plane perpendicular to the web has to be greater than 15 degrees.
Prestressed and non-prestressed bolted connections
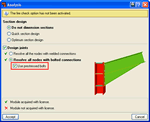
CYPECAD, CYPE 3D and Integrated 3D structures of CYPECAD allow bolted connections to be
designed using prestressed or non-prestressed bolts. This option is located in the Analysis
menu (Analysis > Analyse) or in the joints design dialogue box (Joints > Analyse).
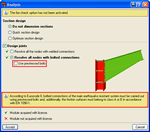
When
the structure is analysed taking into account seismic effects, the program either recommends
or imposes the use of prestressed bolts depending on the selected seismic code. If the code
states the use of prestressed bolts is obligatory, the program selects this option and does
not allow for it to be deactivated. If the seismic code does not state it is compulsory to
use prestressed bolts, the program reminds the user it is advisable to use these as is recommended
by Eurocode 8.
When bolted connections are used, the program also indicates the friction surface
class to be used in case that selected by the user in the design options is not adequate.
If the warnings are not taken into account by the user, it is possible for the prestressed
bolted connection to not be designed by the program. In this case, when the user consults
the joints after the analysis, the program indicates as errors the reasons why the design
has not been carried out.
Bolted connection design
General properties
If during the analysis process of the structure, nodes are detected whose configuration
is adjusted to those types resolved by the program, they will be designed and detail drawings,
3D views, code check reports and take-off of these designs will be provided.
The program designs the dimensions of the plates and stiffeners, the optimum number and
layout of the bolts and the throat thicknesses of the welds required for the correct stress
transmission in the connection.
The program designs the bolted connections using a front plate or a lateral plate:
- Moment connections using front plate. This type of solution is used
by the program for fixed connections between beams and columns, for element splices and
ridge beam connections.
- Simple connections using lateral plates. This type of solution is used
by the program for pinned connections between beams and column webs or flanges, and webs
of other beams (secondary beams).
- Simple connections using front plates. This type of solution is used
by the program for beams supported at column ends forming a pinned connection.
Non-deformable bar ends
When welded or bolted connections are designed, or when the structure is analysed together
with the joints, the program carries out, at each node of the job, the spatial layout of
the bars and its fixity conditions in such a way that, for steel bars, the dimensions of
the nodes are established and generates the rigid ends in which the portions of the bars
are considered to not deform due to them being contained within the node.
Rotational stiffnesses at element ends
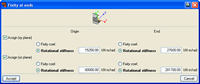
The program allows for fixity coefficients xy and xz or rotational
stiffnesses to be assigned to bar ends (bars or set of aligned bars forming one
element). Defining the rotational stiffness allows for the joints to be modelled and whereby
their stiffness to rotate is fundamental to bear into account, as is in the case of bolted
connections.
For each bolted connection that is designed, the program analyses (for all the acting force
combinations) the rotational stiffness of the end of each fixed element and
suggests a value with which the structure is to be reanalysed. The proposed stiffness will
be the smallest amongst those calculated at each element end, which corresponds to the one
with the greatest positive or negative moment.
After the analysis and for elements fixed to the bolted connections, if the user has not
defined the rotational stiffness or if the introduced value differs in more than 20% from
that proposed by the program, a warning is emitted. This is also displayed as a warning in
the report at the end of the analysis or in the option Show error
messages in the Analysis menu.
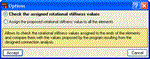
Using the Rotational stiffnesses option in the Joints menu,
the user can manage and substitute the values that were introduced instead of those proposed
by the program (at the ends of elements with moment bolted connections provided by the program).
This option activates a dialogue box with two possibilities:
After assigning the rotational stiffnesses proposed by the program to the desired element
ends, the structure must be reanalysed so the new force distribution due
to the change in the rotational stiffnesses can be taken into account. The program emits
a warning of this situation.
Design criteria for prestressed bolted connections
The shear check in the transverse section of the bolts is substituted for an Ultimate Limit
State (U.L.S.) slip check in the case of prestressed bolted connections and the tension and
slip interaction is analysed.
When the user activates seismic action for the analysis of the structure, the fixed prestressed
bolted connections are designed for Failure Mode 1, i.e., failure will occur due to plastic
failure of the front plate of the connection and not due to bolt failure. Therefore, when the
seismic action is taken into account, bolts are designed using greater diameters to guarantee
enough rotation capacity.
Joint consultation
Following the analysis, the joints that have been designed by the program can be consulted.
CYPE 3D and CYPECAD place different coloured circles at the nodes to indicate whether or
not all the connections of the node have been designed, if there are only a few that have
been designed or if the node does not contain any designed connections.
If the cursor is brought close to a node in which there are connections that have been designed,
an information window will appear indicating the types of connections designed for that node.
By clicking on the node a dialogue box with three tabs is displayed containing the following
information:
- The construction details of the resolved connections
- A report of the checks and take-off of the resolved connections
- Real 3D views of the connections. It is possible to visualise a 3D view of each connection
designed by the program with an isometric or conical perspective. The elements making up
the joint (columns, beams, stiffeners, welds, bolts and plates) are drawn in different
colours. Prestressed bolts and non-prestressed bolts are also represented in two colours
to differentiate between them. The user may also freely rotate and amplify the 3D view.
These characteristics greatly help the user to understand the assembly of the joint. The
3D view of the joints can be visualised by selecting the 3D view tab that appears in the
bottom part of the window that is activated upon consulting the joint.
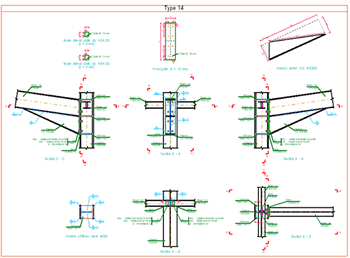
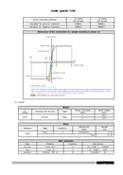
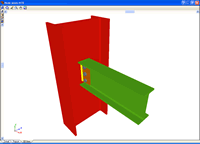
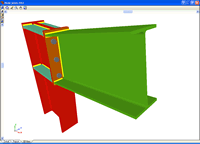
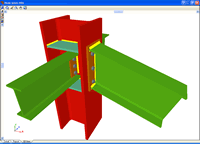
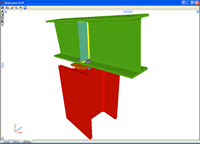
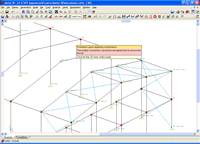
If the cursor is brought close to a node in which there are no designed connections, but
belongs to one of the connections recognised by the program, a window appears informing of
the causes that have prevented that joint from being designed.
Even if the user license has not acquired the joints modules, the program allows the user
to activate the joint design process. Once the process has concluded, the user can see the
3D views of the joints that could be resolved with the non-acquired modules, even though
neither the joint details, check reports nor take-off reports are displayed. When the cursor
is placed over one of these nodes, a warning appears indicating the non-acquired modules
used to design the joint.
Baseplates designed using the Joints II module
The Joints II, Bolted, Warehouses with rolled and welded steel I sections moduledesigns
baseplates on footings, pile caps and slabs.
The Joints II module also designs the baseplate connection points of integrated
3D structures,
if these are located on footings, pile caps, slabs, shear walls, walls, concrete columns
or beams (in the case of these last four elements, they are designed if no other steel beams
or steel bars of the integrated 3D structures connect at that node).
The properties of the
designed baseplates include:
- Baseplate types: Baseplates for rolled steel and welded I sections are
designed.
- Welds: Includes the analysis and design of the welds between the plate,
stiffeners, column and bolts.
- Automatic match: Automatically matches all the baseplates of a job (bearing
in mind the section type, forces and exterior fixities). This way, and without the user
having to intervene, the number of different types of baseplates is reduced, hence obtaining
more uniform results.
- 3D View with highlighted elements and welds: It is possible to obtain
a 3D view on screen whereby the baseplate, column, stiffeners, bolts, factory welds and
insitu welds are displayed in different colours, in a similar manner as to how joints are
represented between I sections. This has been incorporated to help the user understand
how the support is to be assembled.
- Baseplate layout: A layout diagram of the baseplate is generated in
which the details of the designed welds and stiffeners are displayed. This layout diagram
can be included in the job drawings.
- Takeoff and code check reports: Takeoff and code check reports are generated
of baseplates that have been resolved. These are integrated with the rest of joints that
have been designed.
More information on baseplate design can be found in the Baseplate
section of CYPE 3D.
Bolted joints report
CYPE 3D and CYPECAD generate a joints report with the following data:
- Welded connection specifications
- Code
- Materials
- Construction layout
- Checks
- Bolted connection specifications
- Code
- Materials
- Construction layout (includes conditions and possible fastening methods of prestressed bolts)
- Checks
- References and symbols
- Baseplate checks
- Relationship of the designed joints
- Calculations
- Construction detail of each type of joint
- Description of the components of each type of joint
- Check results of each type of connection
- Weld, plate and bolt take-off for each connection type
- Complete take-off of welds, plates and bolts of the designed joints
Bolted joints drawings
The construction details of the joints designed by the program can form part of the drawings
of the structure. The Joints drawings include the following elements:
- Construction detail of the joint
- Schedule with specifications of the welds in steel structures
- Code
- Materials
- Construction layout
- Fastening procedure of prestressed bolts
- Checks
- Reference and symbols table
- Complete take-off of welds, plates and bolts of the designed
joints
CYPECAD and CYPE 3D modules
CYPE 3D modules:
CYPECAD modules:
Modules common to CYPECAD and CYPE 3D: